01
Overview
Our in-house valve assembly and state-of-the-art testing facilities give us complete control over the full manufacturing process allowing us to deliver a high quality finished product.
We can manufacture valves to any design specification, including with your choice of materials, within a very short lead time.


02
MANUFACTURING ACCREDITATIONS
Our focus on quality management dates back many decades – having held the previous BS5750 quality accreditation since 1982, we completed our ISO9001 approval in 2007. We also hold a number of key industry specific accreditations. Additionally, many of our products have passed stringent qualification testing, demonstrating their performance against ASME, ISO and API design codes.

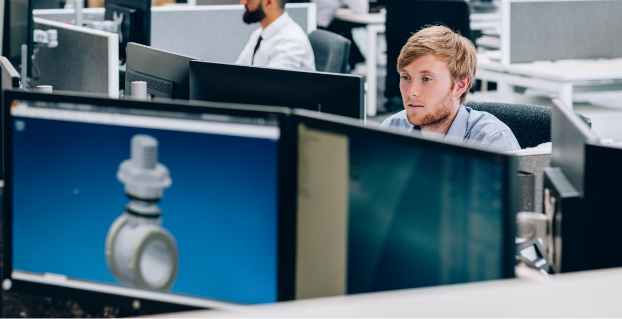
PRODUCT REALISATION & CAD
Our product realisation service forms part of our in-house R&D facility. This has been a key focus for investment and has made many of our new product ranges possible, enabling us to develop bespoke valve products for our clients with highly demanding and sophisticated needs.
QUALITY MANAGEMENT OF COMPONENTS
We use the latest technology and specialist in-house expertise to deliver the same high standards of quality management, testing and inspection for our components as you would expect from our finished valve products.
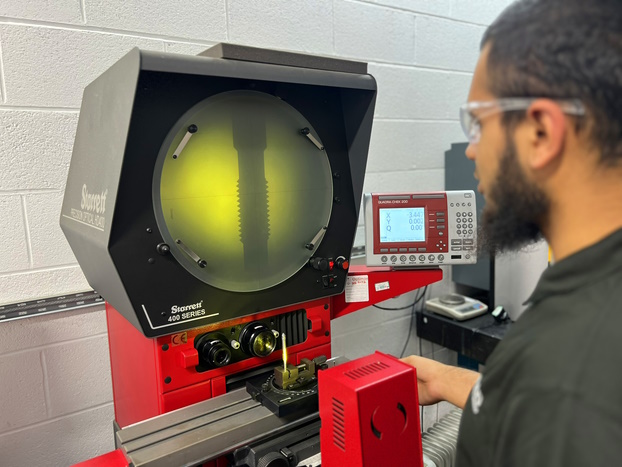
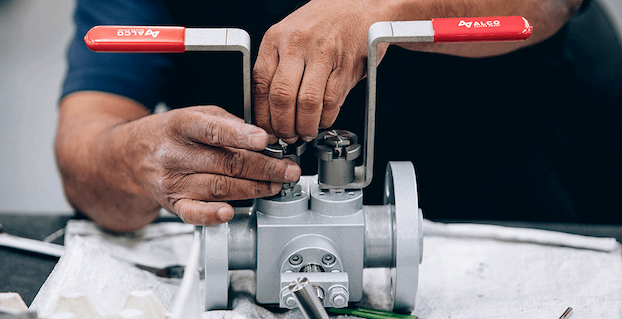
EXPERIENCED IN-HOUSE ASSEMBLY STAFF
Products are assembled by our experienced, highly-trained engineers in Brighouse, West Yorkshire. We have excellent levels of staff retention and continue to recruit the best in the industry, investing in their future development so knowledge is retained and expanded within the business.
IN-HOUSE VALVE TESTING
Valve products are thoroughly tested in our dedicated testing facility before delivery to our customers. Depending on the product requirements, they may be production tested to design code requirements, or extensively tested in purpose built test bunkers using Helium or Nitrogen gases. Additional extended testing at elevated or reduced temperatures is available upon request.
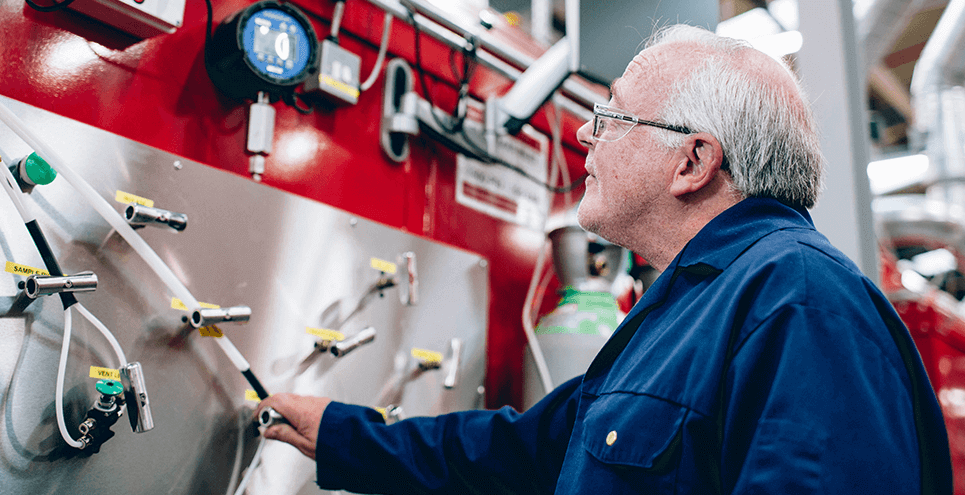
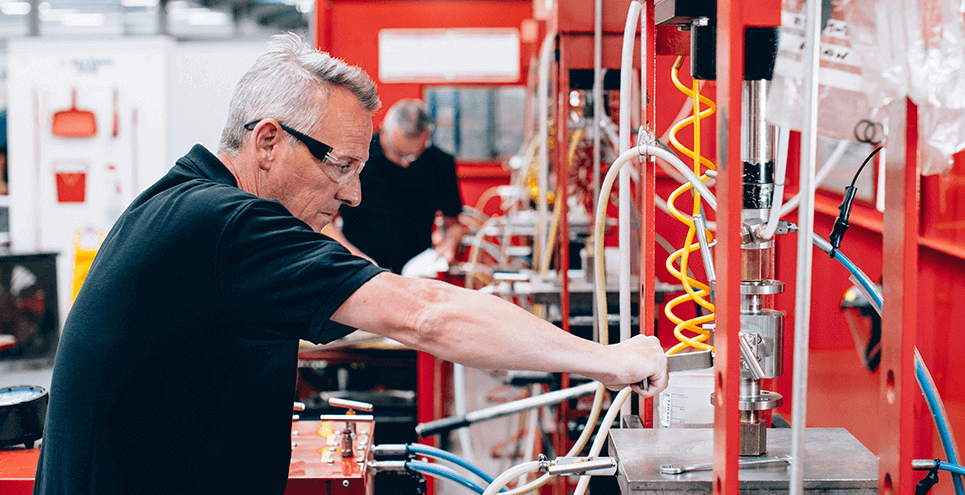
HIGH-INTENSITY, ACCREDITED VALVE TESTING
If valves are for more demanding severe service or critical applications In-house qualification testing can include; cryogenic, hyperbaric or fire testing amongst others. All without the valves needing to leave our premises. Our testing facilities meet the rigorous, internationally recognised standards such as ASME, API or ISO and are supported by 3rd party inspections agencies such as Lloyds, DNV or TUV.
SAFE, SECURE WORLDWIDE DISTRIBUTION
All finished products are safely and securely packaged using foam-in-place packaging to ensure safe arrival of your goods whilst reducing waste and transportation costs. We make every possible effort to ensure that your valve arrives in the “as-built” condition ready to go straight into service.
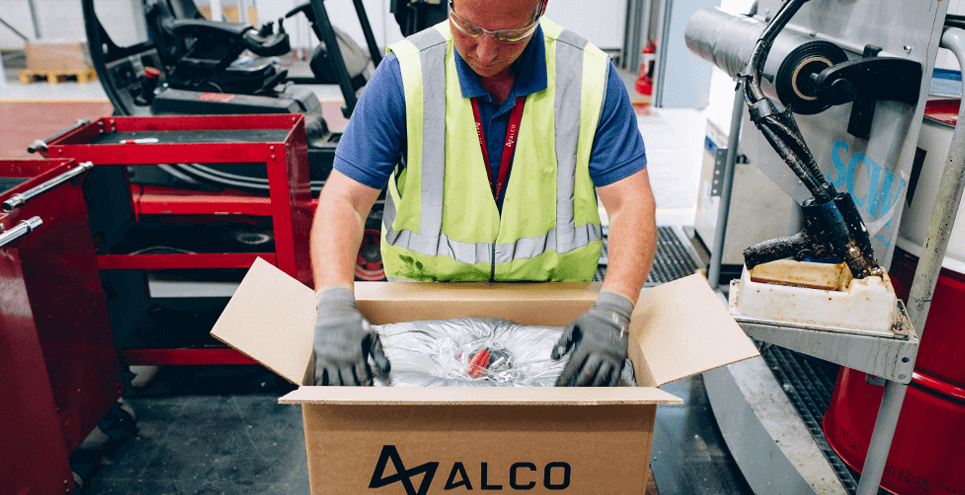
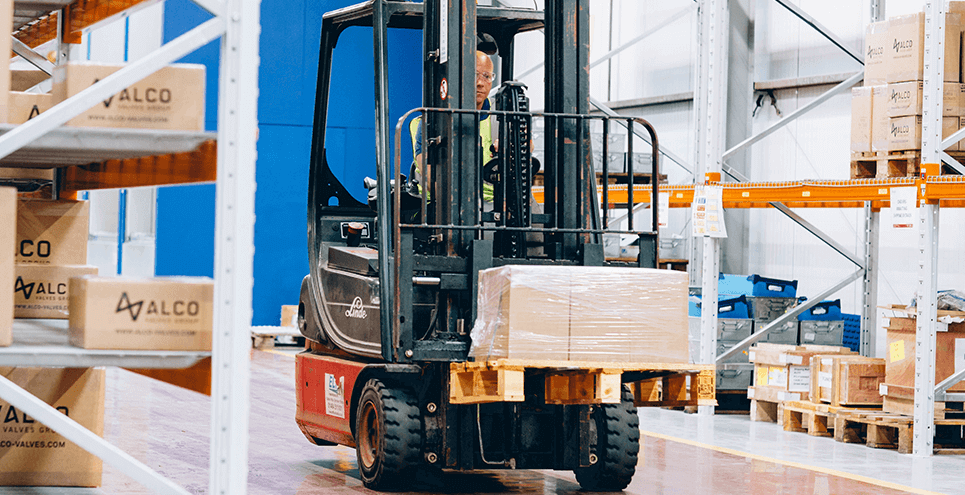
TIMELY DELIVERY FOR CRITICAL APPLICATIONS
We can ship finished products to just about any location worldwide meeting demanding deadlines. Our products includes a range of ready-to-go (RTG) valves with next-day delivery to many parts of the world.
03
VALVE TESTING & COMPLIANCE
TESTING STANDARDS
Our valves are subject to comprehensive testing to ensure that they can perform effectively in the most demanding of operating conditions. We recognise that lives can depend on the performance and reliability of our products and have invested heavily in world-class testing facilities to give you greater peace of mind.
Our extensive facilities range from simple low-pressure testing for our more basic valves, to our new shock-resistant ballistic test bays. These test bay enable us to replicate even the most demanding service conditions, with pressures of up to 60,000 psi for pipework and 21,500 psi for gas and hydro manifold valves.
All our testing bays are fitted with dedicated camera systems which enable us to record or share live testing for remote witness. This allows test engineers or 3rd party inspectors to view our valves under high test pressures in great detail from outside the blast containment.
All of our testing activity is extremely safe and adheres to HSE (Health & Safety Executive) recommendations regulations for operator and witness inspection safety.
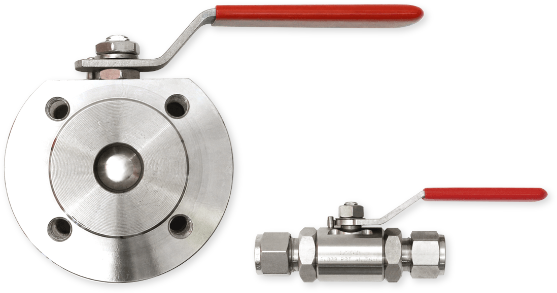
ALCO VALVES TESTING INCLUDES
- Ballistic Impact Testing
- Destructive Testing (DVT)
- Fugitive Emmission Testing
- Cycle Testing
- Fire Testing
- PR2 Testing
- Hyperbaric Testing
- Type Approval Testing
- High/Low Temperature Testing
- Endurance Testing
- Hydrostatic Testing
- Gas Testing
- Torque Testing